The foundry has a long and proven track record in the production of Zamak alloy and in the refining processes of zinc alloys
Our mission
The S. Erasmo Zinkal foundry specialises in the production of zinc alloys for die casting. Over 60 years of industrial experience are the founding pillar of its reliability and manufacturing excellence, that is acknowledged by the market and is continuously being developed and improved, thanks to investments and experiments aimed at ensuring final quality and sustainability of the entire production cycle.
Sustainability, reuse of raw and secondary raw materials and innovation, namely, the “circular economy”, are at the core of the biggest changes of our times, the green deal: of course, S. Erasmo Zinkal leads the field, as it has always massively used production scrap and by-products in its zinc alloys.
Authoritative studies and statistics show that the environmental impact of recovery of these materials sent for melting is twenty times lower than the extraction from ore and subsequent treatment.
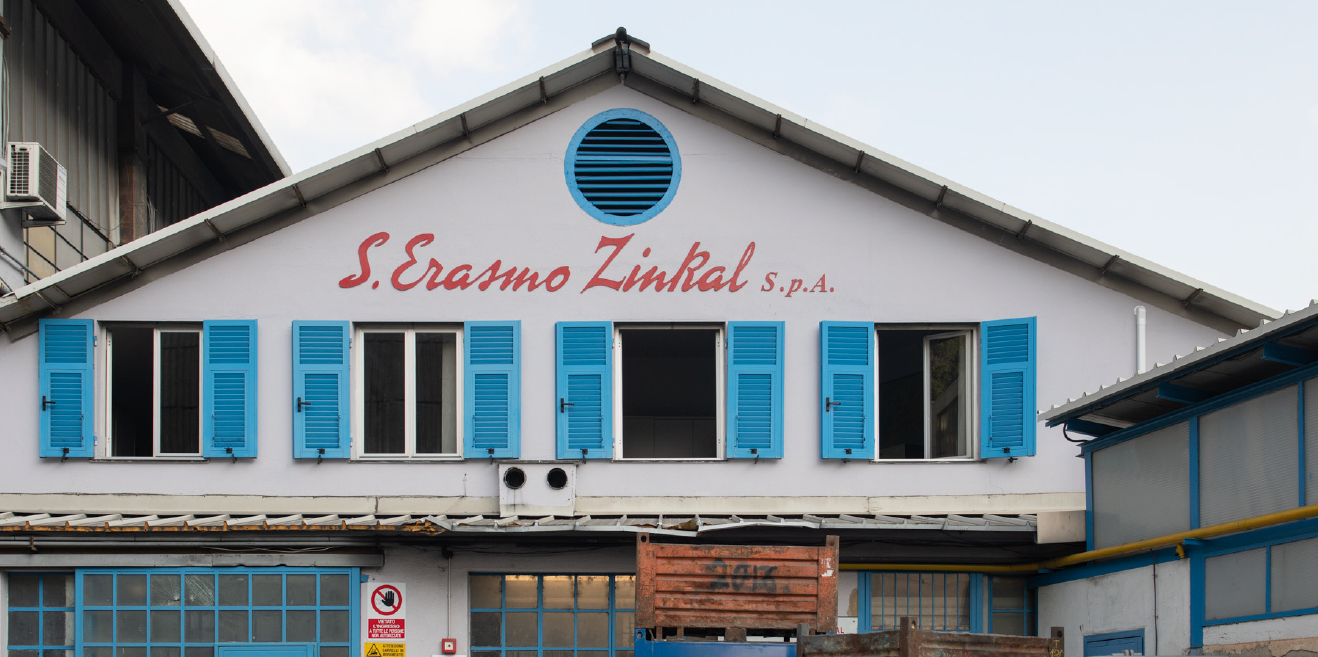
Quality and customer satisfaction
- Zama alloy prices constantly updated according to the performance of the London Metal Exchange (LME);
- Short and long-time supply contracts offered;
- Quality controls performed through spectrochemical analysis with 4 decimal places;
- Assistance provided in identifying the most suitable types of alloys for die-casting requirements
- Logistical organisation for the distribution of our products throughout the country – by our own transport service – and to both EU and non-EU countries, using leading international carriers
- Maritime transport easily organised with the leading shipping companies thanks to our industrial site being close to the port of Genoa
- Continuous administrative assistance ensured by dedicated staff
- Also, dedicated staff provides continuous assistance with regard to evolutions of legislation in health and safety at work and environmental matters
- Commercial promotion networks present both in the national and in foreign markets
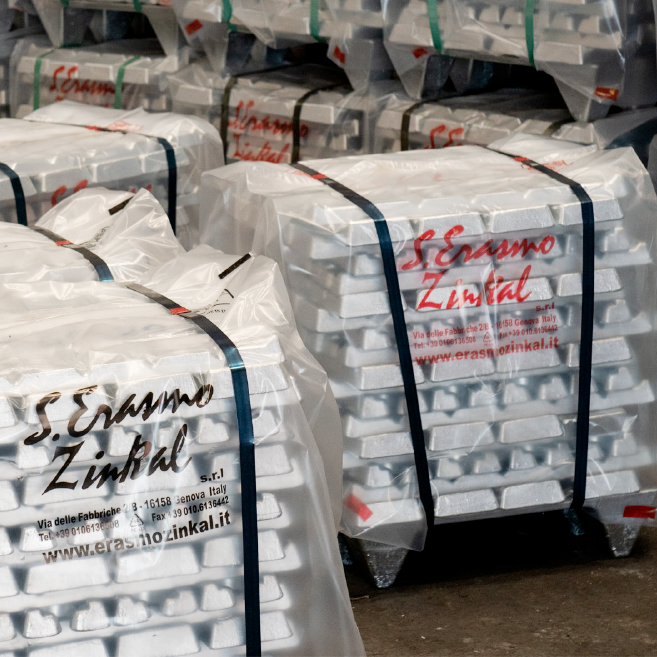
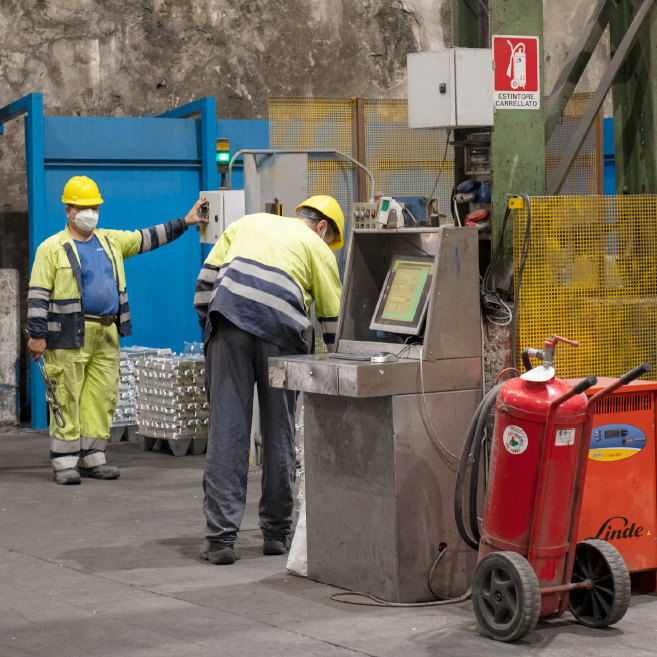
Our sectors of use
Thanks to its intrinsic versatility, the zamak alloy has a very wide range of application, covering various segments of the reference market. The mechanical properties – resistance and ductility – of these alloys are higher than those of many other casting materials such as aluminium, magnesium and brass, and that is why they are used in several product sectors, among which car components stand out.
Indeed, zamak alloys ensure very uniform “shrinkage properties”. As a consequence, the casts generated during the die casting process are very precise and do not require further processing, as they are perfectly prepared for surface treatments.
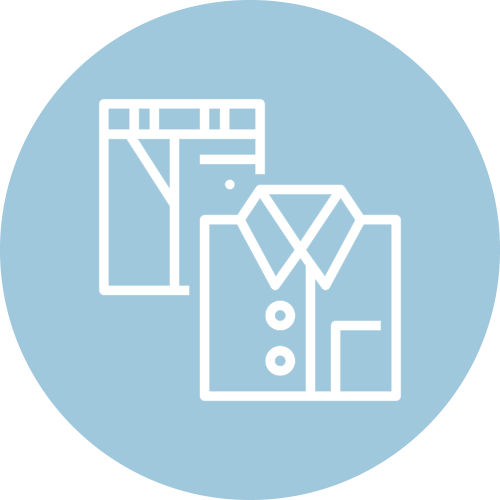
APPAREL
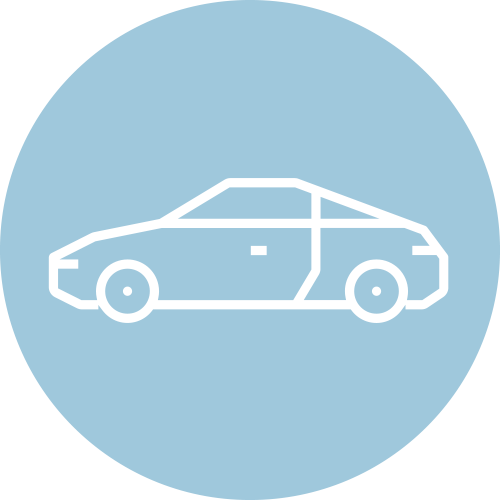
CAR COMPONENTS
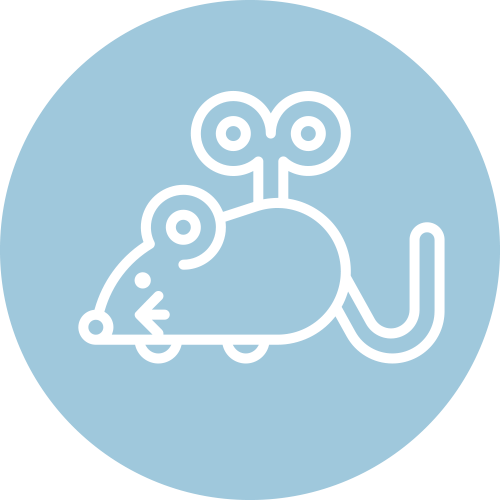
MODEL BUILDING AND TOYS
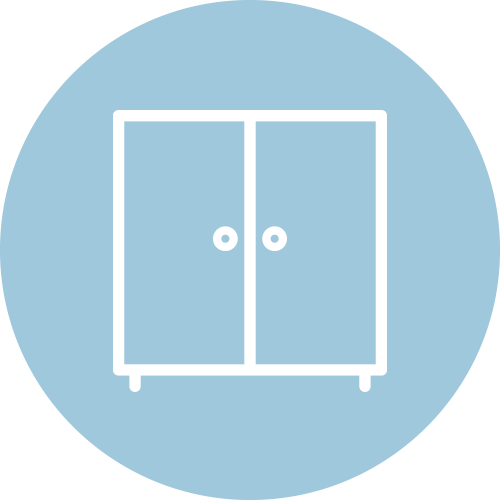
FURNITURE COMPONENTS
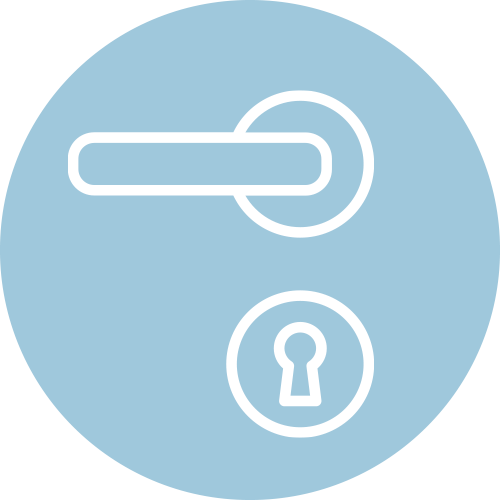
INTERIOR DECORATION COMPONENTS
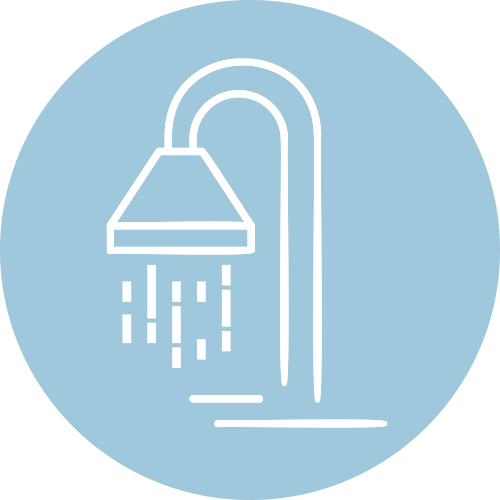
SANITARY COMPONENTS
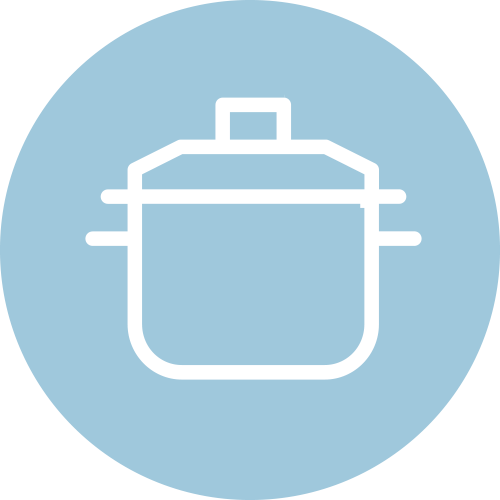
KITCHEN ACCESSORIES
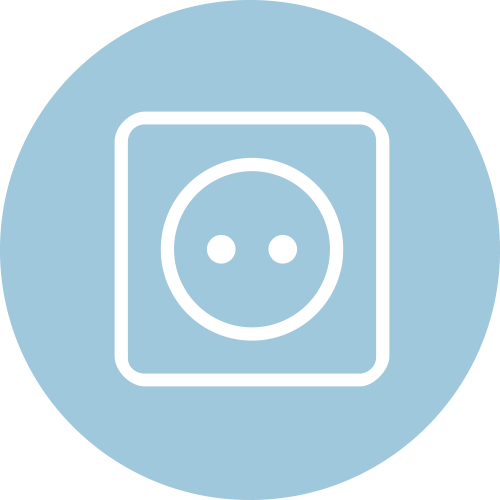